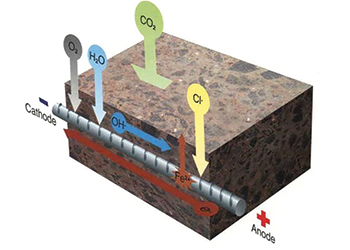
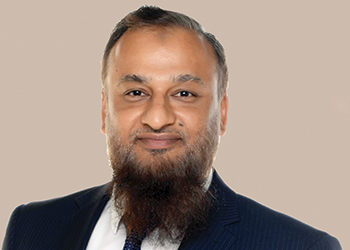
Dr REHAN AHMED of Heriot-Watt University’s Dubai campus discusses the use of carbide-based coatings that can combat corrosive wear, which makes them attractive for the construction industry.
Understanding the scientific principles that underpin natural phenomena – including those involved in corrosion and corrosive wear – has enabled engineers to find technological solutions to improve the quality of human life.
The principles behind the corrosive process have been deployed to provide the necessary surface finish to ceramic bearings used for the aerospace and machine tool industries, while galvanic cells take advantage of the process in electrical batteries. Corrosion, however, compromises the durability and safety of engineering systems. The construction industry utilises two different techniques of corrosion protection: for example, sacrificial coatings of aluminium, zinc or nickel to protect iron, or non-sacrificial coatings to stop the underlying material from being exposed to the corrosive medium.
Thermal spray coatings can be utilised to protect bridges, masts, steel structures against corrosion. Ducas (2006) reported the corrosion protection of an iron bridge with zinc using thermal spray coating process [1].
![]() |
Thermal spray coating technology is a process in which the coating material, which can range from a polymer to a high temperature ceramic such as aluminium oxide, is heated and accelerated to spray on the substrate material to form a coating. The coating thus formed has a lamella structure. The advantage of this coating process lies in the high deposition rates and coating thickness of several millimetres, which makes it attractive for the construction industry. A number of these thermal spray coating techniques and materials are, therefore, currently commercially available to combat against corrosion.
A complication of corrosion arises when it is accompanied by abrasive wear process; for instance in pipelines, the abrasive medium would be sand. In these cases, the sacrificial coatings of aluminium, zinc or nickel could not be used as they have a relatively low abrasive wear resistance.
In some cases, the high operating temperature of these components poses further problems. This is where carbide-based coatings come into their own, with their ability to combat the combination of corrosion and an abrasive environment – a term collectively referred to as “corrosive wear”. Although corrosion and wear individually lead to the material loss and hence influence the structural stability, the synergetic effect of corrosion and erosion is, however, generally far more significant.
Heriot-Watt University is investigating the use of tungsten carbide (WC)-based metal-matrix-composite (MMC) coatings using a state-of-the-art high-velocity oxy-fuel (HVOF) process for a range of applications requiring protection against corrosive wear. Published literature on the topic indicates that although the abrasive wear resistance of WC-Co coatings is relatively high, its corrosion behaviour is complex due the formation of different microstructural phases, such as W (tungsten), W2C (tungsten semi-carbide) and Co6W6C (eta-carbide), etc formed during the coating deposition process.
Different combinations of WC, such as WC-CrNi (tungsten carbide-chromium nickel) and WC-CrC-CoCr (tungsten carbide-chromium carbide-cobalt chromium), have been compared in the published literature for industrial applications. The university’s current research concentrates on taking advantage of newly developed nanocomposite WC-Co coatings where the carbide size of WC is varied from several microns to nanometre scale.
![]() |
FIGURE 2: Hardness (HV0.3), wear rate and expected corrosion resistance of thermally sprayed WC-based MMC coatings. |
Nanocomposite materials offer higher mechanical strength and coatings manufactured from nanocarbides are thus attractive for a variety of tribological applications. In this research, WC coatings are also compared for the variation in the metal matrix by using a combination of layers of WC-10 per cent NiCrBSi (nickel chromium boron silicon) and 40 per cent NiCrBSi coatings.
Figure 1 illustrates the typical microstructure of these coatings. The sliding wear performance comparison in accordance with ASTM G133-02 is illustrated in Figure 2, along with their respective hardness values. The general indication is that WC-Co coatings perform better in abrasive wear when compared to WC-NiCrBSi coatings, although the corrosion performance of the former is expected to be lower.
Understanding this balance between corrosion and abrasive wear resistance is the key in optimising the design of engineering systems against corrosive wear. This understanding will enable the engineers to design and manufacture the correct composition of carbide coatings for specific applications requiring resistance to corrosive wear.
It is worth noting that the corrosion resistance of these coatings is dependent upon the corrosive environment while their wear resistance depends on the abrasive medium. Hence understanding of the underpinning wear and corrosion mechanisms enables designers to make the right choice of coating and substrate material for specific corrosive wear applications.
References
[1] PL Fauchais, JVR Heberlein, MI Boulos, “Thermal spray fundamentals-From powder to part”, Springer, ISBN 978-0-387-28319-7, 2014.