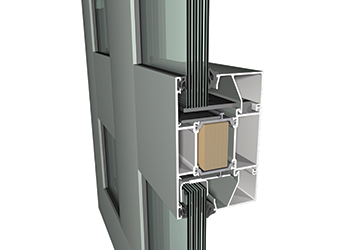
Lisec showcased its ‘bestsellers” in the fields of software, cutting, tempering, insulating glass manufacturing, glass processing, logistics and handling at glasstec 2016 in Dusseldorf, Germany, which was held last month.
In line with its motto, “best in glass processing”, for this year’s edition of the leading trade fair for glass products, machines, production and processing, the Austrian specialist in the field of flat glass processing and finishing presented some of its striking innovations such as its Aeroflat tempering furnace, a new software for efficient processing and a new concept for the production of insulating glass units with thermoplastic spacers (TPA).
Aeroflat is a tempering furnace designed to cut costs and enhance reliability. According to Lisec’s project manager Manfred Spreitzer, in creating the new system, Lisec’s development team had to literally start from scratch to project to redesign the tempering furnaces in order to save manufacturing costs and increase the process reliability.
The new Aeroflat is technically more sophisticated and weighs almost 50 per cent less than its predecessor. This weight reduction brings benefits in its assembly (lighter engines and tools as well as simpler handling) and for the customers due to lower transport costs and generally lower production costs.
Amongst the many advantages of the new Aeroflat are the reduction in waiting time when the types of glass are changed; wear-resistant ceramic components; significantly shorter heating time; no cooling of the heating zone required in case of glass breakage; and identical cycle time for coated and uncoated glasses.
In addition, operators can be trained in only five days and 50 per cent less staff is required compared to conventional plants. Also tempering of double-sided coated and printed glass sheets is possible, while thermal tempering of glass, from 1 to 10 mm, is possible.
At glasstec, Lisec promoted its Industry 4.1 software, which allows transparent and efficient production processes in glass machining and processing.
The integrated network from the preparation of offers to the delivery supports the optimisation of the production process and allows seamless product tracking, says Spreitzer. Integrated quality checks along the production process, beginning with the incoming goods inspection to the final check at the end of production, allow a consistent quality report, thanks to the networking which may act as a quality proof for a specific order.
Predictive and preventive maintenance is possible that helps to prevent unplanned downtimes and thus increases the availability of the plants. Data can be collected and evaluated in real time.
Fast lane concept
Lisec has developed an entirely new concept for the production of insulating glass units with thermoplastic spacers. The key features of the concept, which has been designed with cycle time, high quality and accuracy in mind, are that it does not require manual intervention under normal circumstances from the cutting to completion of the insulating glass unit. It provides for one applicator and achieves a cycle time of 35 seconds for standard triple-glazed insulating glass (size: 1 sq m). It has a high speed due to an innovative LiftOver system.
Core plants of the fast-lane TPA line include the assembly press, CleanSeal technology and the fully automatic glass removal system UTS.
The press used in this concept is a completely new development. The AGP (which stands for assembling, gas filling, pressing) press is fast and offers high pressing accuracy. The tolerance for insulating glass up to a size of 2.5 sq m is a maximum of 0.5 mm in terms of element thickness. The press can be used in a very large range of applications due to the fact that it can process elements of 350 kg per linear m (and up to 200 kg per m for the first two glass sheets). A particularly important feature of this press is that it supports all glass sheets up to triple-glazing insulating glass at any time during the assembly which prevents any sliding down.
The AGP also features the Lisec gas filling technology where the gas, by means of a laminar flow, is filled from the bottom across the entire width of the insulating glass element without bending the glass during this process.
CleanSeal technology, Lisec’s sealing solution, features a highly dynamic self-regulatory servo-controlled dosing system which detects temperature variations and changes in the viscosity, among other things, caused by differences between batches and downtimes and it adjusts itself. New in the concept is the patented full support belt, which is able to process elements weighing up to 350 kg/linear m.
Furthermore, using the UTS system, the finished insulating glass units are automatically lifted on the TPA line. Insulated glass units remain in the curing buffer until they are cured so that any manual handling (packing) won’t have any influence on the accuracy of the element thickness.
Also presented at glasstec was the revised RS cutting technology 2016 (grinding and cutting in one operation), claimed to be the world’s fastest solution in terms of production runs with a high percentage of coating (above 60 per cent). For typical cutting patterns, Lisec’s ESL-RS is 10 per cent faster than the fastest cutting plants in the market, Spreitzer claims.
The plant can be combined with new innovative glass storage solutions such as the package loading system and the revolutionary FlyOver glass loading and a breaking plant designed for the application, ranging from the simple breaking table to the fully automatic high-performance tandem (double) and triple dispatch.
“And the best thing is: Lisec plants are indefinitely extendable. Thus, our customers’ security of investment remains guaranteed even in case of future increases in capacity or any shifting of the fields of work,” says Spreitzer.
Lisec has also paid particular attention to quality in production, downtime management and part tracking. Increasingly shorter delivery times combined with high quality requirements generate pressure in producing flat glass free from defects.
“At Lisec, this approach starts with the truck which delivers the raw glass that is unloaded by a ground-based or overhead storage system. This system is combined with a fully automatic warehouse management, glass cutting and breaking plants as well as an autonomous residual plate management. In terms of glass sorting, our customers may choose between the approved stationary solution which consists of a glass buffer and a shuttle and the mobile sorting system MSB which may be loaded and unloaded fully automatically,” says Spreitzer.
“The insulating glass elements are generally very sensitive until the sealing material is cured. In order to prevent deformations, tolerance errors or even the destruction of the product, Lisec’s UTS carefully removes the elements and takes them to the curing zone, at which end it is possible to perform the dispatch as usual,” he adds.
At glasstec, Lisec also presented a logistics innovation. The new tilting shuttle SHL facilitates layout plans even in the most confined spaces. It covers standard inclination of two to six degrees but also tilts horizontally (90 degrees) if required. The tilting shuttle uses SHL’s rail system and may therefore be operated with speeds of up to 300 m per minute and accelerations of up to 3 m per sq sec.
Based in Amstetten, Lisec has been offering innovative individual and overall solutions in the field of processing and refining of flat glass for more than 50 years. It develops and produces glass cutting and sorting systems, individual components and entire production lines for the production of insulating and laminated glass as well as machines for the processing of glass edges and tempering systems.