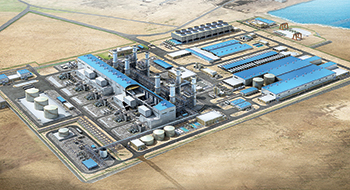
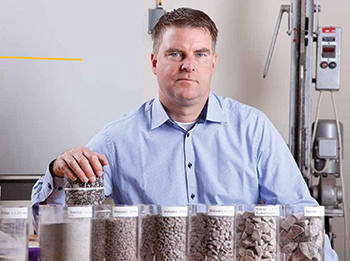
Dynapac equipment has long been a familiar sight on road building and other construction sites around the world including the Gulf region.
The company has a history of dedication to machine performance and ranks among the technology leaders in the field of soil, asphalt and rockfill compaction, milling and paving.With its Technology and Application Center (TAC), Dynapac aims to become the leading partner for compaction, milling and paving applications, offering the best performing products backed by unmatched knowledge.
The TAC is located at Dynapac’s machine performance testing facility in Karlskrona, Sweden.
According to manager Fredrik Åkesson, one of the aims of the TAC is to raise the level of application knowledge in the infrastructure construction and other construction sectors. “We want to influence decision-makers, planners, and specification writers in these industries, as well as local governments, and road administration and homologation organisations,” he says.
He points out that Dynapac compaction, milling and paving know-how and solutions can be used to build strong, sustainable road networks and minimise traffic disruptions due to repair and maintenance work.
“There is huge potential for achieving direct and indirect savings in time and money for everyone. Our capability to influence decision-makers will steadily enhance our brand image and help us become the first choice for major infrastructure and other construction projects worldwide,” he adds.
“We achieved our current position as a technology leader through decades of research and full-scale testing, in-house and in the field,” says Åkesson. “Compaction and paving is a science in itself and, here at the TAC, we have a unique store of accumulated and documented knowledge that can help to ensure the optimal compaction and paving result and, thus, a durable foundation for every type of project.”
Extensive know-how spread throughout the Dynapac organisation enables to provide expertise and support for high level projects and major customers worldwide.
This know-how will now be focused in the TAC, where the testing facilities are situated.
At the TAC, the test facilities include indoor and outdoor test areas and a laboratory. The indoor test area has enough space to accommodate even the largest single drum rollers, enabling full-scale testing to be performed under controlled conditions with no interference from the weather. This ensures reliable results, regardless of the time of year, and allows accurate machine compaction performance comparisons to be made. Outdoor testing is performed from May to September to reduce the influence of the weather and thus ensure reliable results.
A dedicated test engineer ensures repeatability and reliability in handling the test equipment and reports the data to the research engineer for analysis. Test results are passed on to the product design and development department to ensure that new products provide the highest possible compaction, milling and paving performance.
The TAC has a fully-equipped materials laboratory conducting ongoing research into materials and their behaviour during compaction, milling and paving.
“Our strategy is to achieve a balanced mix of short-term daily activities and longer term research and investigation that will lay the foundation for future products and applications,” explains Åkesson. “Initially, the TAC will put a lot of effort into training people in Atlas Copco customer centres around the world in machine selection and methods.”
Day-to-day activities will primarily consist of end-user support and training. The centre will provide training on construction materials as well as on machine and material interaction and other issues relating to compaction, milling and paving. It will also generate tools for training – there is already a comprehensive compaction and paving manual.
In the longer term, the TAC will continue the work already in progress in the organisation based on the principles and basic theory of compaction, milling and paving, and the development of quality measurement, documentation systems and methods.
Technical support
The TAC will provide technical support for helping customers with machine selection and methods for upcoming projects, as well as assisting with problem-solving in ongoing projects. The centre can assist in clarifying job specifications or provide input for new specifications based on an extensive compaction and paving database compiled over many years of testing activities.
For high level projects and major customers, the TAC’s application expertise, resources and experience are available in the form of direct consultation and support.
Input from sales and service staff at Dynapac is a vital source of information that will enable the TAC to monitor trends and developments around the world.
“Our entire focus is on the interaction between machine and material, that is, the application of the equipment,” says Åkesson.
“Different jobs require different machines and settings. Depending on the type of job and the quality requirements, different ways of operation may also be required. It is essential to take all of these parameters into account in order to make sure the right machine is used for the job and that it is utilized in the most efficient way. Only then will the machine meet, or hopefully exceed, the end-user’s expectations.”
In many cases, it is possible to improve the performance of an existing compaction solution. This provides savings in project time as well as cost for compaction. Changing conditions on the jobsite, such as natural variations in the material composition, or the need to change layer thickness, can in most cases be handled by changing the machine settings or other operational parameters.
“When it comes to paving our recommendations can result in significant improvements to the customer’s paving process,” continues Åkesson. “The process needs to be continuous and every link in the chain must interface correctly with the next to achieve the desired result. The number of tons of asphalt mix you can deliver to the paver decides your paving speed in relation to your layer thickness and paving width. In turn, the paving speed and the cooling time of your asphalt mix must be matched with sufficient compaction capacity, that is, using the correct rollers in sufficient numbers.”
While the the TAC is not responsible for development of new Dynapac equipment, the product Design & Development department will benefit continuously from the results of the TAC’s application research and machine performance testing activities. Viable research projects will be transferred to the design and development team as input for new products