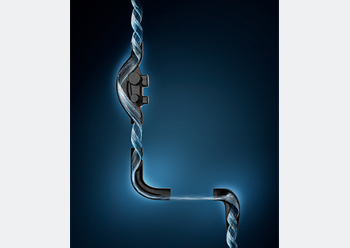
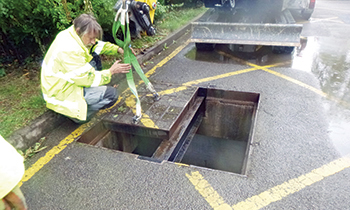
Drainage and sewerage companies across the globe are increasingly specifying composite access manhole and trench covers where manual handling is key, says a leading UK-based manufacturer.
Accessibility is a pre-requisite for almost every drainage and sewerage application. However, the weight of conventional heavy steel access covers can make removal and replacement time-consuming and cumbersome, says David Holmes, technical director of Fibrelite, a global leader in the manufacture and development of glass reinforced plastic (GRP) composite manhole and trench covers.
“While once steel or concrete were the only options, a new breed of composite cover is making the world beneath our feet more accessible than ever,” he says.
![]() |
After ... lightweight Fibrelite covers. |
Designed by Fibrelite, the new, lightweight alternatives are claimed to have an unrivalled strength-to-weight ratio, and provide the same load-bearing performance as their conventional counterparts.
“In fact, due to the lightweight properties of composite material, Fibrelite GRP access covers are approximately one-third lighter. This makes them simpler and safer to install and manoeuvre by hand, and eliminates the need for specialised lifting equipment,” he remarks.
Holmes says Fibrelite is seeing an increasing number of enquiries for GRP custom cover solutions in water and wastewater applications and more specifically in locations where there are manual handling concerns.
“Our design and manufacturing capabilities allow us to offer custom turnkey solutions that can replace failing metal and concrete covers in-situ, thus eliminating the need for costly installations and extended site closures. The evidence is in the numbers, more than 5,000 bespoke covers have been successfully installed in the UK, Europe, US, and even Antarctica,” he states.
Holmes points out that traditional, heavy covers are also prone to corrosion, with sand and water ingress being a major problem for operators and site owners. In the long term, this can lead to costly damage and the need for regular maintenance, he says.
“In contrast, GRP composite requires no maintenance and is resistant to corrosive materials – making it an ideal solution for many drainage and sewerage applications.
“Furthermore, composite covers can be designed to fit almost any size, shape, aperture and load rating requirement – enabling effortless like-for-like replacement. It is even possible to specify different colours and custom covers that feature a specific logo or branding.
“This freedom and flexibility make GRP composites a natural fit for the demands of modern construction,” he remarks.
Fibrelite invented the first composite access cover in 1980 and is now specified by the majority of major oil companies, including locally: ExxonMobil, Total, Adnoc, Woqod, Enoc and OiLibya.
Fibrelite’s high-performance composite covers can be custom designed to suit any specification in the company’s dedicated facilities in the UK, the US and South East Asia. A rapid design-to-delivery process, and a responsive local distribution network also guarantee fast turnaround times, he adds.
Since 2013, Fibrelite has been a part of OPW (a Dover company) allowing the company to offer an unprecedented portfolio of complementary best-in-class products.
Fibrelite is a global manufacturer of highly-engineered GRP composite access covers capable of taking up to 90-tonne loads whilst still being light enough to be lifted by hand. It is renowned for its high-quality technical support and service.
Initially developed almost 40 years ago and now an industry standard for petrol station forecourts, Fibrelite covers are increasingly specified for both new and retrofit work in a variety of industries in more than 80 countries around the world.