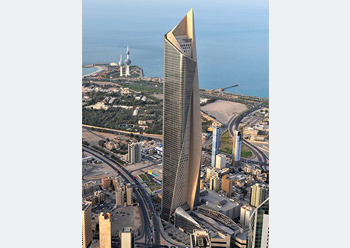
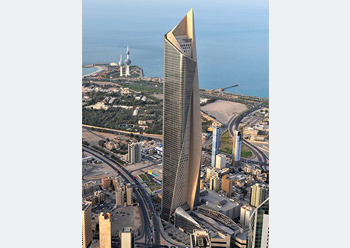
The Gulf region has its fair share of impressive concrete projects that have gained recognition for excellence in concrete design and construction, thanks to their innovative use of concrete technology, says the American Concrete Institute (ACI), a leading authority and resource on concrete worldwide.
Among such projects are the Al Hamra skyscraper in Kuwait, the third Bosphorus Bridge in Turkey, and the South Marina Yacht Club in Qatar.
“Each build stands out for architectural and engineering merit, creativity, ingenuity, sustainability and resilience, functionality, and ground-breaking use of materials and construction solutions,” says a spokesman for ACI.
![]() |
Al Hamra Tower ... to enlarge the tower’s entrance, five major columns were pushed 25 ft to compose a lamella structure. |
Each of these projects was recognised as a winner at the annual ACI Excellence in Concrete Construction Awards in 2015, 2016 and 2018, respectively.
“The awards programme elevates winning projects from a local level, and highlights them on a global scale, following fierce competition from the best projects around the world,” the spokesman says, adding that winning an excellence award speaks of the innovative use of concrete design, materials, and construction.
Elaborating on these projects he says, Al Hamra Tower, which is located on the site of Kuwait’s first cinema, has built on its legacy by creating the nation’s tallest skyscraper. The landmark offers dynamic mixed-use facilities for investors, tenants, and visitors alike.
The project comprises a sculptural office tower, which anchors a commercial complex comprising offices, a health club, and a high-end shopping mall. The development was constructed on an 11,000-sq-m site, and at its tallest, the office tower reaches 412 m high. The car-park consists of 11 levels with an approximate capacity of 2,000 spaces. Not only is the tower the tallest building in Kuwait, but also provides the country’s largest office space. Additionally, it is the tallest concrete structure in the Middle East, says the spokesman.
The project used self-compacting concrete (SCC) of strength ranging from C-40 to C-80 N/mm for a height of 412 m (triple blend cement, microsilica and flyash) pumped.
“The two main walls flare out in opposite directions, which makes one of the walls extrude out of the building centre. Due to this, the designers built in an opposite twist, so when the concrete creeps over time, the building will take its correct shape and straighten on its own. Most skyscrapers settle in a vertical direction, but in the Al Hamra tower, settlement will happen in the vertical and horizontal directions,” the spokesman points out.
Because of Kuwait’s dry weather, the contractor had to use huge pumps to pour the concrete in order to get the concrete up to the top at 414 m in less than 15 minutes.
“The use of SCC provided for the foundation and substructure elements greater than 1 m deep. The SCC was a proportioned mix with reduced coarse aggregate size, increased paste content, and the addition of a super-plasticizer and air-entraining admixtures.
“In order to enlarge the tower’s entrance, five major columns were pushed 25 ft to compose a lamella structure, and the sweeping and curved columns are 40 ft in height, with four connections to the ground, lift lobby, to each column, and to the whole parts of the structure,” he explains.
Al Hamra tower is owned by Al Hamra Real Estate Company. The architect and engineer of record on the project was Skidmore, Owings & Merrill (SOM), while the general contractor, concrete contractor, and concrete supplier was Ahmadiah Contracting and Trading Company.
Third Bosphorus Bridge
![]() |
The Third Bosphorus Bridge in Turkey ... 104,000 cu m of C50/60 concrete was used to construct the four pylons. |
This bridge has eight lanes of motorway and two lanes of railway on the same level. A bridge of firsts, this is the widest suspension bridge in the world at 59 m. It is also the longest spanning bridge with a railway system on it, with a main span of 1,408 m.
Elaborating on the project, the spokesman says: “The reinforced concrete pylons of the Third Bosphorus Bridge are the tallest suspension bridge pylons in the world, with a height of more than 322 m. The tower structures are built with reinforced concrete up to a height of 305 m, and the rest is a steel saddle for the main cables.
“The compressive strength of the concrete used in the project is classified as C50/60, and it fulfils various durability requirements, providing at least 100 years of service life under rough environmental conditions. A total of 104,000 cu m of concrete was used for the construction of the four pylons of the bridge, including their foundations.”
According to the spokesman, the chloride migration value of the concrete used during the project was below 3x10-12 sq m/s, and the chloride content was below 0.1 per cent of binder content, in order to provide higher chloride resistance for durability purposes.
Fresh concrete was permitted to have a temperature of between 10 deg C and 28 deg C after pumping. The initial setting time was tailored through the admixtures within pours, especially during the first 208 m of slipform construction. The binder composition consisted of 50 per cent ground granulated blast furnace slag (GGBFS), and 50 per cent CEMI42,5R LA cement due to the high durability requirement. Natural sand, crushed sand, and two coarse limestone aggregates were used in the mixture design.
“Concrete pumping to the top height of 208 m was completed with a single pump line for each pylon, without any transfer point. After 208 m, the formwork system was changed, and between 185 and 160 cu m of concrete was poured in a single pour. During the entire project, pumpability of the concrete was continuously monitored by checking and measuring the pressure in the hydraulic system of the pump and the pipe line. This method allowed continuously recording the condition of the concrete and pumping equipment, and the suitability of the mixture design,” he explains.
Because of this systematic approach, concrete was delivered by pumping to the highest man-made reinforced concrete structure in Turkey.
The project owner is ICA (IC Ictas-Astaldi JV), while the architect and engineering firms that oversaw work on the project were structural engineer Michel Virlogeux, and T-Engineering. IC ÇTA was the general contractor and Akçansa Çimento Sanayi ve Ticaret A, the concrete contractor and concrete supplier.
South Marina Yacht Club
![]() |
South Marina Yacht Club in Qatar ... Slag cement was incorporated into the concrete mixture to limit the temperature of hydration. |
Occupying a prominent position over the water of Lusail Marina District, Qatar, the iconic two-storey South Marina Yacht Club takes its inspiration from movement and aero/hydro-dynamism, two concepts associated with yachting.
The building features post-tensioned slabs spanning 15 m, which provide an open indoor space, and a cantilever spanning 5.3 m all around (tapered at the free end to reduce dead load) to provide distinctive panoramic wide terraces.
Concrete for the substructure had a design strength of 75 N/sq mm (10,800 psi). The building is supported on a 700-mm raft with piles founded in Simsima limestone.
“The perimeter wall was continuously placed to ensure integrity. Slag cement was incorporated into the concrete mixture for the ground slab and suspended pit slab to limit the temperature of hydration, thus minimising cracking.
“Other durability-enhancing factors for these slabs included corrosion-inhibiting admixtures, increased concrete cover, and reduced water-cement ratios,” the spokesman says.
To provide corrosion protection, the piles were constructed with a concrete mixture comprising 60 per cent slag cement and eight per cent microsilica, and the specified concrete cover was 75 mm (3 inches).
The building was selected as the green commercial building of the year in 2016 by the Qatar Green Building Council. Additionally, the project team only contracted with local suppliers to enhance the sustainability of the Qatar economy. Some 60 per cent of the concrete components were produced locally, and 11 per cent of the concrete components were from recycled materials, the spokesman says.
Owned by Qatari Diar, Lusail Real Estate, the South Marina Yacht Club was designed by Chapman Taylor Espain and built by a joint venture of Ceinsa and Al Jaber Trading & Contracting. The concrete contractor was Al Wataniya.
“It is inspiring to see projects like these continue to shape the concrete industry and raise the benchmark in the industry,” says the spokesman.
Further photos and videos of the projects can be viewed at ACIExcellence.org.
ACI continues to be the resource worldwide for the development, dissemination, and adoption of its consensus-based standards, technical resources, educational and training programmes, and certification programmes. It shares a commitment with individuals and organisations involved in concrete design, construction, and materials to pursue the best use of concrete.