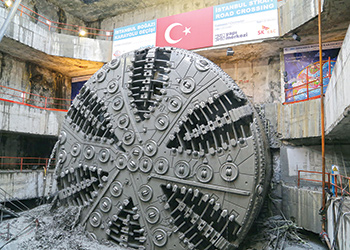
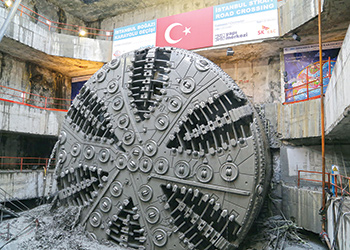
Major projects in Turkey and the Gulf are relying on Herrenknecht of Germany for its high-tech TBMs to create deep tunnels.
Tunnel boring machines (TBMs) from German specialist Herrenknecht have achieved key milestones and awards for their operators in the region over the past year.
One the latest milestones was reached on one of the boldest tunnelling missions – under the Bosphorus Strait linking the European and Asian sides of Istanbul in Turkey.
In last August, in the presence of a high-level audience that included Turkish Prime Minister Ahmet Davutoglu, a Herrenknecht mixshield TBM with an excavation diameter of 13.7 m pierced the target shaft wall on the European side of the mega Turkish city exactly to plan.
“After 16 months of tunnelling under the Bosphorus Strait, the emergence of the drilling giant was an engineering and emotional triumph for the building contractors, a Turkish-South Korean joint venture between Yapi Merkezi and SK Engineering and Construction,” says a spokesman for Herrenknecht.
Launched from the Asian side, the 5.4-km-long underpass for the two-storey Eurasia road tunnel was a huge endurance test for ultra-modern tunnelling technology, he adds.
![]() |
The Bosphorus project overview. |
Never before has such a large, high-performance tunnel been built underground under such complex and extreme conditions, the spokesman claims.
TBMs are a high-tech mechanised alternative to conventional methods of design-and-build mining, drilling and blasting tunnels through everything from soft ground to hard rocks. They form circular tunnels through the rock, and can install concrete linings along the drilled sections to reinforce the bored tunnel and stabilise the ground.
The unique 3,300-tonne TBM used on the Bosphorus project was specially designed at Herrenknecht’s headquarters in Schwanau and was launched in April 2014. With a gradient of five per cent, the large-format Mixshield tunnelled down to the deepest point 106 m below the Bosphorus, where the water pressure was 11 bar.
“Combined with a highly variable, wear-intensive underground, this places extreme demands on the giant cutting wheel’s excavation tools. This necessitated a range of different safety features – trialled in previous undertakings and further developed for pioneering projects – that only Herrenknecht can provide.
“The particular challenge was to develop a cutting wheel that allows safe replacement of the excavation tools from the inside even with the huge external pressure,” explains Werner Burger, head of engineering at Herrenknecht.
The result: a cutting wheel accessible from the rear through narrow working chambers. The tools can thus be changed safely by the crew through special lock systems under atmospheric pressure conditions.
In addition, the TBM was fitted with special equipment for the use of saturation divers. It achieved excellent top performances under the Bosphorus of up to 92 m per week.
From late 2016, around 100,000 cars a day are expected to cross between the continents using the Eurasia Tunnel on two roadways, one above the other. The new tunnel infrastructure is the first direct link between the historic Golden Horn peninsula on the European side and the port area on the Asian side. It is expected provide relief from the chronically congested traffic in Istanbul and reduce the journey time from 100 minutes to just 15 minutes.
![]() |
The two TBMs used on the Abu Hamour Southern Outfall Project in Doha, prior to delivery from the Herrenknecht plant. |
Meanwhile, in Saudi Arabia, TBMs used on the Makkah Haram Sewer Line project have helped the owner of the project, National Water Company, earn the GSTT Award in the special International Projects category conferred by the German Society for Trenchless Technology.
For the project, two Herrenknecht EPB Shields (3,510 mm diameter) are being used to drive the much-needed sewers with segmental lining directly under the holy city of Makkah.
Tight curve radii of 80 m are being driven over distances of 1.5 and 1.8 km. Concrete segments with two sealing profiles and an HDPE (high-density polyethylene) in-liner provide additional protection for the particularly secure removal of sewage through groundwater,
For the project, Herrenknecht had to put together a tailor-made service package. Since only Muslims are allowed to enter Makkah, a special remote monitoring system customised for the project was developed together with Saudi Binladin Group (SBG) of Saudi Arabia.
Machine operators from Herrenknecht can support the advance around the clock. The TBM’s control cabin was, therefore, duplicated and its data transmitted from the jobsite in Makkah directly to the offices in Schwanau. Prior to tunnelling, the customer’s site crew was trained at the Herrenknecht plant on the curve radius of the machine’s set-up.
“We have to work under time pressure in tight curve radii under Makkah’s busiest ring road and through holy groundwater. For this unique challenge, we needed a unique solution. Herrenknecht gave us a complete package – including 24/7 support,” says Ibrahim Balaban, general manager at SBG’s tunnelling division.
![]() |
One of the two TBMs used on the Makkah Haram Sewer Line project. |
Qatar projects
Elsewhere in the region, close to two dozen TBMs from Herrenknecht are at work in Qatar on the massive Doha Metro project. Some 21 TBMs have been delivered to Doha over the past year and most of them are currently operating on the Red, Green and Gold lines beneath the vibrant city.
Early this year, the first TBM on the Red Line was lifted from one station site to another. For transporting the TBM on the Red Line, efficient logistical preparations were carried out before the lift and transfer, ensuring a safe transportation process. A 1,600-tonne crane was hired to lift the huge high-tech machine, while a special hydraulic trailer – 6.3 m wide and 18 m long – equipped with 192 wheels was employed for transportation. Traffic lights were temporarily dismantled, and a specialised ISF (Internal Security Force) force escorted the convoy.
Among other recently projects, two of Herrenknecht TBMs were also employed for the Abu Hamour Southern Outfall Project in Doha to drive a tunnel 20 to 30 m underground.
Commenting on the project, the spokesman says: “Services laid underground are indispensable for supplying the growing world population. Water, sewage and other infrastructure have to be built up and extended to match the increasing requirements of growing cities.”
While Doha lies in an arid zone receiving scant rainfall, the fact that it lies just metres above the groundwater table level, means the densely populated capital city experiences flooding during any rains, explains the spokesman.
The Abu Hamour Southern Outfall project is a comprehensive drainage scheme by Qatar’s public works authority Ashghal to cover an area of 170 km and ensure improved drainage for the southwestern section of the city.
The EPB Shields with a diameter of 4.47 m were designed for Doha’s soft limestone soil. The precast concrete segmental lining technique – a technique with single concrete segments which are combined to a closed ring – was used for the first time in Qatar to excavate the tunnel.
In July last year, the two TBMs successfully finished the 10-km-long tunnel under the Qatari capital without disrupting the traffic above ground or damaging any buildings in the area.
“A central pumping station near the New Doha International Airport pumps the surplus water through a pipe with a capacity of up to 19 cu m water per second. After heavy rainfall, it will transport the water to the Arabian Gulf and, therefore, prevent flooding and relieve the existing pumps,” says the spokesman.
Herrenknecht is a leading provider of holistic technical solutions in mechanised tunnelling, building on the experience of more than 2,850 projects worldwide. It offers solutions for all diameters, in all geologies and in all areas of application – railway, metro, road, utility, pipelines, hydropower, mining and exploration.
The group, with its headquarters in Schwanau, consists of Herrenknecht (the parent company) and 80 subsidiaries and associated companies working in related fields in Germany and abroad.