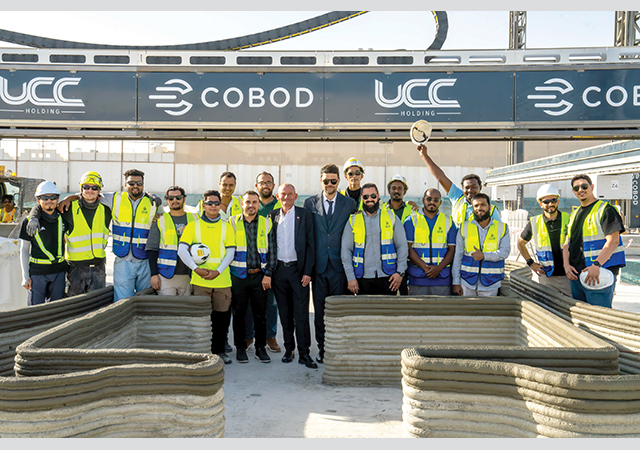
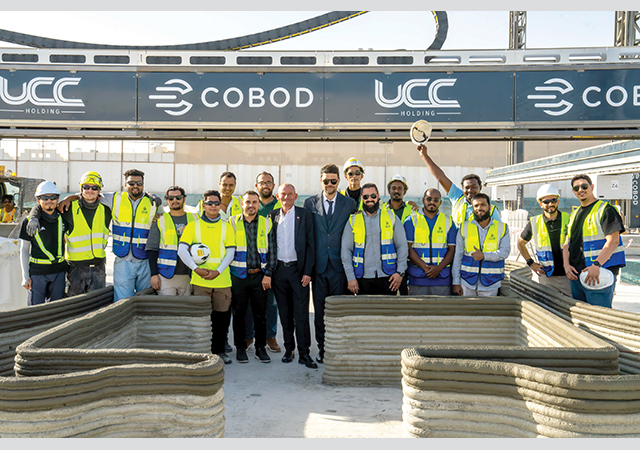
UCC Holding, in partnership with Qatar’s Public Works Authority (Ashghal), has announced that it has officially commenced the printing phase of the 3D printed schools project – marking the launch of the world’s largest construction development using 3D printing technology.
The project involves the construction of 14 public schools in Qatar, including two built using 3D printing technology, each with a built-up area of 20,000 sq m – totalling 40,000 sq m.
This is 40 times larger than the largest 3D-printed building constructed anywhere in the world to date, UCC Holding claims. The two schools are designed as two-storey buildings on plots measuring 100 by 100 m each, making this project an unprecedented model for future-ready educational infrastructure in Qatar and across the region, it adds.
To realise this unprecedented scale, UCC Holding has commissioned Cobod, a global leader in 3D construction printing based in Denmark, to supply two customised BODXL printers, each measuring 50 m long, 30 m wide, and 15 m high – roughly the size of a Boeing 737 hangar – making them the largest construction printers in the world.
Following extensive preparation - including site development, equipment assembly, and operational simulations - printing operations have officially begun.
![]() |
The BODXL printer from Cobod measures 50-m long, 30-m wide, and 15-m high. |
In a LinkedIn Post, Cobod Founder Henrik Lund-Nielsen says that the first to the two BODXL printers has now been installed and is printing at the UCC Holding school building site in Doha. “The world has never seen such a large 3Dconstruction printer before, and it is more than four times bigger than the second biggest printer.
On its own, this printer can produce a 1,500 sq m (16,146 sq ft) footprint up to five floors equivalent to a five-floor building of 7,500 sq m,” he states.
A second printer with identical measures was expected to arrive last month.
UCC Holding has assembled a dedicated 3D construction team consisting of architects, civil engineers, material scientists, and printer technicians.
Over the past eight months, this team conducted more than 100 full-scale test prints using a BOD2 printer at a dedicated trial site in Doha, developing concrete mix designs, validating performance under local climate conditions, and engineering a custom print nozzle to ensure precision and smooth extrusion.
In May 2025, the team completed intensive training alongside Cobod engineers, covering printer operation, print sequencing, structural layering strategies, and live quality control. This milestone marks a major leap in Qatar’s local capacity for advanced construction technology, solidifying its role as a regional hub for innovation and engineering.
Compared to conventional construction methods, 3D printing offers multiple environmental, social, and economic advantages. It significantly reduces raw material waste and minimises concrete usage, cutting carbon emissions. On-site printing also reduces transport needs, mitigates supply chain risks, and accelerates project delivery. With operations scheduled at night to avoid high temperatures, the process also ensures better concrete performance while reducing dust and noise, UCC Holding states.
Architecturally, the schools are inspired by the natural desert formations of Qatar, with curved, flowing walls resembling sand dunes. This design is only made possible by the geometric freedom that 3D printing offers - enabling organic, parametric forms that would be difficult or cost-prohibitive using traditional construction methods.
The schools are expected to be completed by the end of this year.
A Cobod 3D construction printer was also utilised to build the world’s first on-site 3D printed large water tanks, which were completed in Kuwait last year by Abyan Building Construction Company, a prominent player in Kuwait’s construction industry and distributor and operator of Cobod 3D construction printers.
According to Cobod, the 3D construction printer helped achieve a 25 per cent savings on the amount of concrete and reinforcement used compared to casted tanks.
Benefitting from the speed and design freedom of 3D construction printing. the tanks were set up faster, more economical, and sustainable than when using traditional formwork.
The tanks, measuring 4.5 m in height and with a diameter of 7 m, were 3D printed with low-cost concrete in just five days and only contained microfibres for the reinforcement of the tank walls and no traditional reinforcement meshes. The tanks were printed with a low-cost real C40/50 concrete mixed on-site using the D.fab solution and related printing equipment invented by Cemex and Cobod, where 99 per cent of all raw materials used are locally sourced.