
IN THE previous tech talks, MH Hydraulics FZC, a leading hydraulic solutions provider in the Middle East, focused on oil contamination. We identified the importance of clean hydraulic oil and various ways to prevent oil contamination.
Following up on our TechTalk#2 article (How to prevent contamination in your equipment), TechTalk#6 will help you better understand how a desiccant breather can be used as a first line of defence in preventing contaminants from ruining your equipment especially on gearboxes.
Lubricant contamination is one of the leading causes for machine failure, and contamination can begin before the lubricant ever enters the machine. Gearboxes, pumps, and reservoirs must “breathe” when the air expands and contracts, and when air is drawn in when hydraulic components activate.
Each time a unit breathes in, it brings with it all sorts of small debris and moisture, depending on the operating environment.
Studies have shown 50 to 70 per cent of lubricant contamination can come from outside the equipment.
Studies show it costs about 10 times as much to remove contamination as it does to exclude it.
There are two primary types of contamination:
• Dirt: If the atmosphere is contaminated, oil will become dirtier and lubricant quality becomes compromised. Particulate contamination, once inside an operating system, will accelerate the generation of new contaminants due to machine wear. These contaminants damage critical components and act as a catalyst for oxidation, further degrading the condition of lubricants.
• Water: If the atmosphere is humid or has frequent temperature fluctuations, the oil is probably filled with moisture and lubricant quality is compromised. Often, plant washdown activities are responsible for inducing conditions that lead to moisture ingression and corrosion.
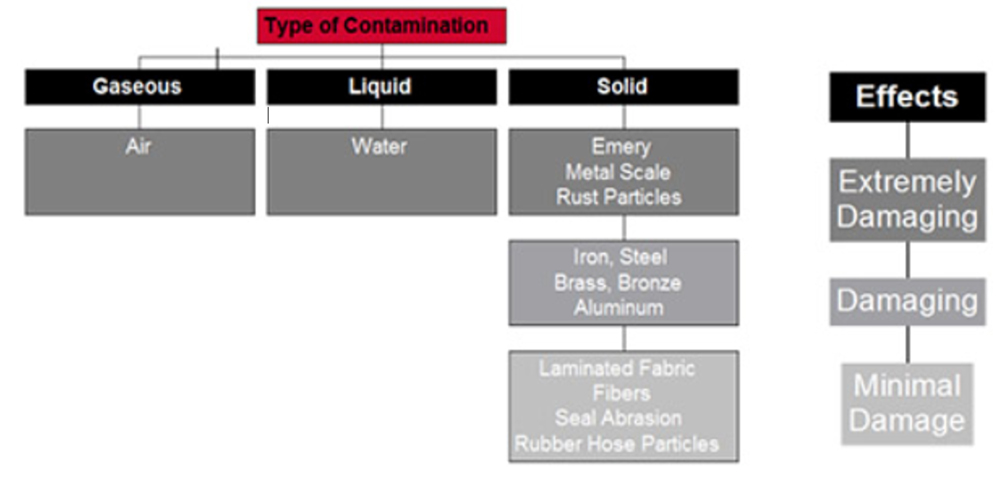
Over time, the effects of this contamination can be damaging to the equipment, lubricant, and causing hydraulic pumps and valves to wear prematurely resulting in hydraulic system failures and damaged system components. Thus, maintaining and controlling clean oil is one of the best investments to maximise equipment and lubricant life.
WHAT IS A DESICCANT BREATHER?
As most equipment and machines are designed to ‘breathe’, protecting the inflow of ambient air is vital for protection and reliable operation. As a first line of defence, we use desiccant breathers.
Before we can define a desiccant breather, we need to understand what a desiccant is. A desiccant is defined as a hygroscopic substance (material that attracts and holds water molecules) that induces or sustains a state of dryness in its vicinity.
A desiccant breather is a unique air filter and water vapour removal system. It combines a drying media with a combination of filters to prohibit water and microscopic particulates from entering the system, and to remove water from the reservoir to prevent condensation.
• The working: Desiccant breathers vary in design and construction. Some work by using a three-stage design to help ensure the interior of your equipment stays clean and dry. Incoming air is cleaned and dehydrated through an initial solid particle filter, a container of silica gel and another solid particle filter.
As our diagram shows how our desiccant breathers work:
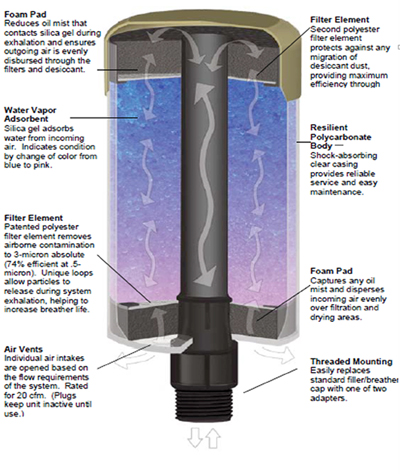
1. As the machine breathes, contaminated air enters the desiccant breather and goes through the first solid particle filter. This is typically filtering out particles two microns or greater.
2. Next, the outside air is dehydrated through a container of silica gel desiccant which extracts the water vapour in the air.
3. Finally, the outside air passes through a third two-micron solid particle filter at the bottom of the desiccant breather.
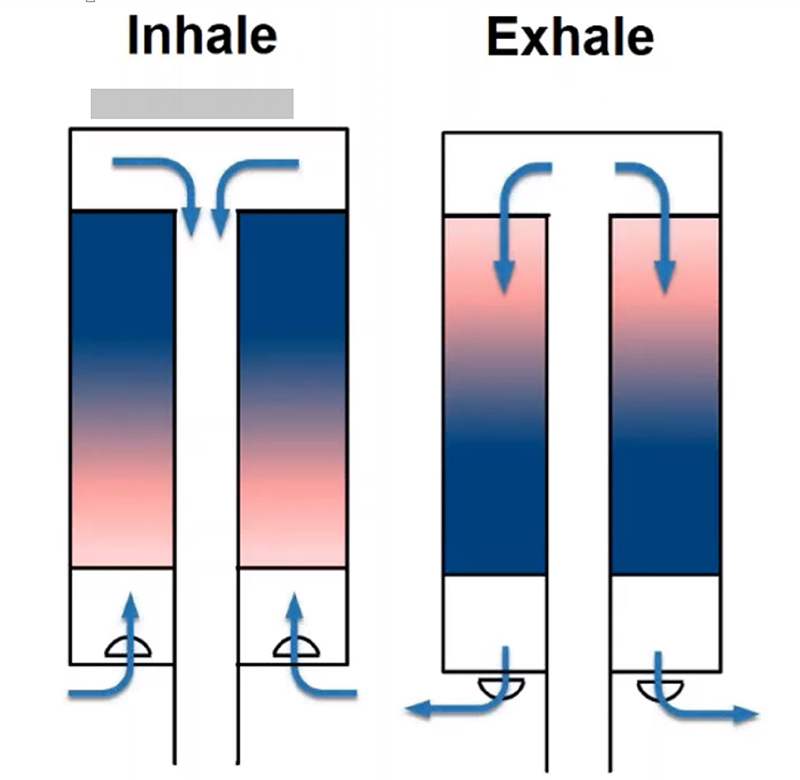
GEAR BOX CONTAMINATION CONTROL
Gearboxes exist in a variety of formats, but all require lubrication because they all have moving components that transmit power through rotation.
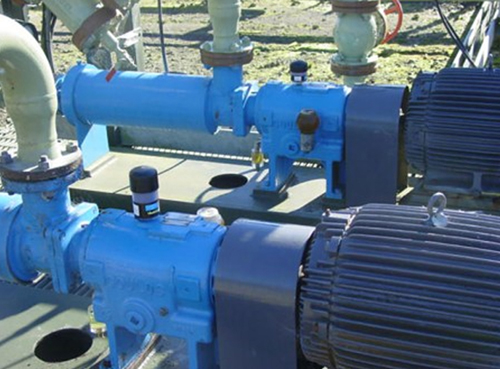
With all moving and revolving parts, gearboxes are extremely vulnerable to malfunctions if contaminated or improperly lubricated. This means that contaminants can not only cause a breakdown in the health of the lubricant (and thus a failure in the lubricant’s ability to perform efficiently) but will also interact with the moving surfaces to cause wear, leading to component failure.
A few common contaminants include dirt, hard particles, water, heat, chemical compounds, improper lubricants, and other environmental debris.
Contamination ingress occurs in a few predictable places on a gearbox: The seals and standard OEM breathers. Additionally, contamination can occur during maintenance, such when refilling or replacing lube. Operating conditions also impact contamination rates; wet surroundings will increase the chance of moisture contamination, while dry, windy circumstances may force silica-based contaminants into outdoor equipment.
Desiccant breathers are commonly installed to enhance contaminant protection. It is wise to install a high-grade breather or exhaust tube in your industrial gearbox. This can help eliminate moisture and airborne debris before they infiltrate your equipment and lead to costly repairs and operational down time.
![]() |
![]() |
We also recommend installing, 3D BullsEye View port, to accurately monitor oil level, water and/or sediment, colour changes in lubricants/oil, and general visual oil condition.
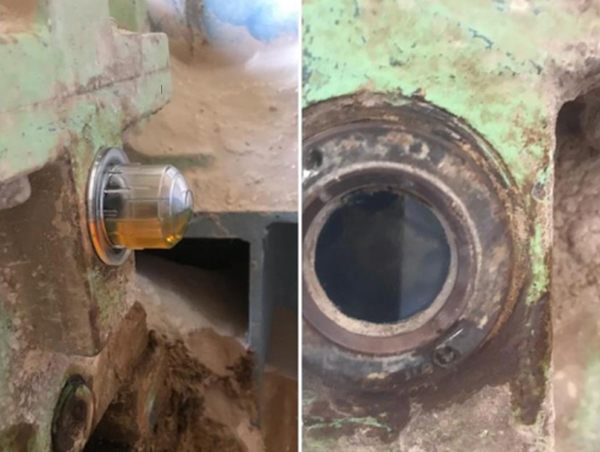
A 3D BullsEye level indicator. Right, a traditional sight glass
CASE STUDY
Professor Ernest Rabinowicz spent much of his time at MIT researching machine wear and what he referred to as loss of usefulness. Professor Rabinowicz is known for his work in tribology, the study of the design, friction, and wear of interacting surfaces such as bearings. He found that approximately 50 per cent of lost equipment usefulness is due to mechanical wear and another 20 per cent is due to corrosive wear.
The National Research Council of Canada furthered the understanding of the cause of mechanical wear by concluding that although several wear mechanisms exist, 82 per cent of mechanical wear is caused by particle contamination.
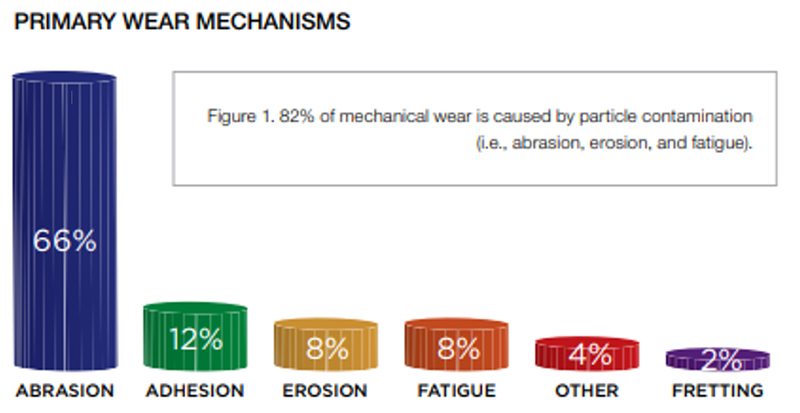
It stands to reason that if particles are the root cause of most of the wear occurring in machines.
Moisture contamination must not also be overlooked. Water causes rust and corrosion, promotes oil oxidation, contributes to sludge and varnish formation, and destroys the lubricant’s film strength.
Furthermore, studies show it costs about 10 times as much to remove contaminants than it does to exclude it.
APPLICATIONS OF DIFFERENT TYPES OF BREATHERS
Des-Case Breathers provide simple, yet dependable protection from moisture and particulate contamination in lubricants and equipment across multiple industries and applications. These versatile breathers are five times more effective than the leading non-desiccant breathers, providing optimal defense against humidity for your applications.
BENEFITS
The best operations and maintenance practices focus on preventing contaminants from entering their equipment, rather than trying to remove contaminants after damage has already occurred.
The benefits of treating the cause of abrasive and corrosive contamination include:
• Elimination of water contamination through the breather.
• Removal of water contamination of the reservoir.
• Prevention of rust and corrosion.
• Increased oil life.
• Improved lubricant performance.
• Increased oil filter life.
• Reduced abrasive wear.
• Reduced rebuild/replacement costs.
• Reliable production from equipment.
• Reduced machine downtime.
CONCLUSION
An array of desiccant breathers is available for various applications based on varying moisture levels, flow rates and working environments. Each type based on target levels of cleanliness, service life, and visibility for inspection and maintenance.
Since contamination is such a major contributor to machine and bearing failure, this low-cost system saves the cost of replacing bearings and gears.
Prevention is always a better choice than shutting down to fix a problem after it occurs.
* This article is provided by MH Hydraulics