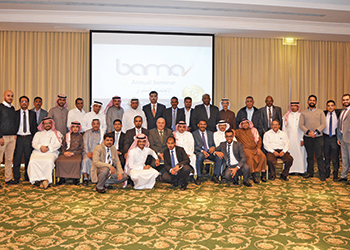
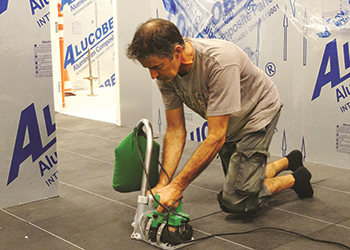
Leister Technologies rose to the challenge when an expanding food company looked to build a floor that could withstand the rigours of a fast-paced kitchen environment.
Tools from Leister Technologies have helped addressed challenges on numerous flooring projects around the world.
Among such projects, Horequip Food Service Architecture from the Netherlands and the US office of Leister Technologies rose to the occasion when called upon by a client to help realise his dream of expanding his catering company.
When the leaders at Puff ‘n Stuff made the decision to build a second, state-of-the-art facility in Florida, the US, it searched for a flooring solution that could withstand the everyday rigours of a fast-paced kitchen environment.
“Those in the food service industry understand that commercial kitchen flooring is subjected to many demands day-in and day-out,” says a spokesman for Leister Technologies. “These environments are often bustling with numerous personnel in relatively confined spaces; furthermore, the flooring is subjected to spills, which can lead to a slippery surface. Therefore, safety is the preeminent factor when determining which material should be used in a kitchen’s design.”
Warren Dietel of Puff ‘n Stuff turned to Horequip, a company with over 20 years of experience in the design and development of turnkey kitchen solutions, for a flooring solution.
Horequip’s proprietary flooring solution chosen for the project is a resilient flooring material, manufactured using recycled PVC and provides a non-slip surface as well as benefits such as sound absorption, flame retardance, resistance to chemicals, oils, grease, and cracks and is watertight and waterproof.
According to Mario Peters of Horequip Food Service, the secret to the quality of the flooring “lies in the correct application and installation”.
Horequip, therefore, flew in an installation team in order to install the flooring themselves using Leister flooring equipment. However, the challenge it faced was the voltage power: the 230/240 V Leister flooring equipment was useless with the 110/120 V voltage in the US.
Horequip’s crew foreman Frans Hamelijnck required reliable and trustworthy 120 V equipment that could work with the Horequip resilient flooring system – however based on his previous experience with Leister tools and the tight timeline, he decided to stick with Leister. Hence, Horequip approached Leister Technologies’ team in Chicago to lease equipment and the latter delivered a Triac ST, Unifloor E and Groover in time for the project’s estimated start date.
The scope of work included wall-to-wall installation of the 20 by 20-inch PVC tiles in the 22,600-sq-ft facility. The installers managed to install and seal 1,076 to 1,615 sq ft of tiles per day. Working 12-hour shifts and six days per week, the team estimated the project would take a maximum five weeks to complete.
During the course of the project, Leister kept direct contact with Horequip to ensure the equipment was working as intended. Leister also tested Horequip’s material samples in its lab in Switzerland, in order to adjust the equipment settings appropriately, for use on the soft recycled material.
For the Groover, which was used throughout the entire project, Horequip requested Leister for additional blades, which were more suitable for the recycled material than the standard ones with the automatic grooving machine. This allowed the Horequip team to work with the machine on a lower setting.
Once the grooves were milled and the floor was vacuumed and cleaned of debris and dust, the team was able to systematically weld the tiles together using Leister’s Unifloor automatic welder, rendering the floor watertight and waterproof. While Unifloor tackled the lion’s share of the welding, the team used the Triac ST hot-air tool to manually weld the cove – where the floor meets the wall. The Triac ST allowed access to hard-to-reach places and the ability to accomplish all detail work.
After four weeks of installation, and over 8 km of welds, the floor was ready. According to Peters, the client was enthusiastic about the welded flooring solution.
“Although the equipment was not shipped pre-set at the optimal settings, Leister provided the appropriate guidance to ensure a positive experience working with both the equipment and with the company,” he says.
And in Hamelijnck’s words: “Leister’s tools are good...now I know its service is too.”
The project involved personnel from multiple countries, who spoke numerous languages, and came from different cultures; the teams from Horequip and Leister rose above all obstacles while working toward one common goal.
This is precisely the work scenario in the Gulf region, says Fabian Beermann, division manager at BMC Gulf, Leister’s sales and service partner in the UAE, which has worked alongside the Swiss manufacturer to rise to the challenge of numerous projects in the region.
Dubai-based BMC Gulf is one of the UAE’s leading suppliers for pipes, fittings and valves as well as welding machines and equipment for the processing of semi-finished thermoplastics materials.