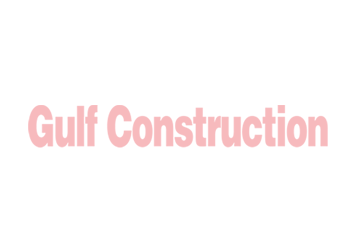

A VISION to build an efficient and technologically-advanced ceramics production facility that will rank among the best worldwide is now close to being realised as the finishing touches are being put to the world-scale factory in Saudi Arabia.
Work on the mega Future Ceramics factory in Dammam is fast progressing with overall civil works being 96 per cent complete. It entails an initial capital of $40 million for the first phase and a total investment of $100 million when completed.
The project was envisioned some six years ago, following which intensive research was undertaken to ensure the success of the ambitious development, right from selecting the ideal location and the most advanced technologies to scouting for the right partners to execute the project and ensuring that the power required would be available for the facility, according to Mazen Al Hammad, managing director and chief executive officer of Future Ceramics.
“We wanted to build an ultra-modern, efficient and technologically-advanced facility that is the best available anywhere and benefits from the very latest technological advances in the tile industry,” Al Hammad comments.
“The intention is to create a series of new brands for the region including Elite Porcelain and for our production to be also sold overseas through partnerships with other leading companies where quality, competitive pricing and creative designs are essential. Our strategy is that about 25 per cent of our capacity will be destined for export markets and the remainder for the GCC,” he adds.
The project is being constructed in several phases over a 277,500 sq m area in the second industrial city of Dammam. In the first phase, the ceramic and porcelain plants, storage warehouse and boundary walls and gates are being constructed.
The ceramic plant covers an area of 27,951 sq m with a 23,731 sq m provision made for future expansion; the porcelain plant spreads over 32,550 sq m allowing 49,333 sq m for expansion and the storage and warehouse is being constructed over 20,700 sq m.
The factory has its own in-house power generation facility and water supply and treatment facilities for its operation.
During the start-up phase, the capacity will be 40,000 sq m per day divided between single-fired tile and through-bodied and glazed porcelain tiles. These last two product types will be manufactured on two lines each with a capacity of 10,000 sq m per day.
Future Ceramics is in contact with several Italian designers to ensure that the company has access to the best creative ideas that are suited to the requirements of Saudi Arabia and the Middle East and for production development.
Elaborating on the progress of work on various components of the project, project manager Raed Mousa says: “Work on the ceramic plant is 98 per cent complete, while the porcelain plant and the storage warehouse have reached 92 per cent and 96 per cent completion, respectively.”
Modern Design and Engineering Consulting (MDEC) was tasked with the responsibility of creating the designs for this industrial landmark. Gulf Consult is the project consultant and was also recently awarded the contract to redesign for the remaining electromechanical work for the project. The firm has a project management team comprising eight engineers supervising all civil, electromechanical and fabrication and installation works on the development.
Eastern Trading and Contracting Company (ETE) is the main contractor for all the civil and electromechanical works of the project, valued at SR68 million ($18.13 million) and SR42 million ($11.2 million), respectively. ETE launched work on the project in May last year and is close to finishing the various components of the development.
All fabrication of support structures and erection works for the advanced equipment including carbon steel and stainless steel piping network for both the ceramic and porcelain plants are being done by AJ Corporation. The task involves detail engineering, procurement, fabrication, sandblast painting and installation of some 2,000 tonnes of equipment.
Road works have been awarded to Ar Rehan Al Arabia, which is currently working on backfill operations on site.
All the structures that house the ceramics and porcelain tiles as well as the storage facilities comprise prefabricated steel buildings have been supplied by Zamil Steel.
The production lines including a 28-m-high technology tower will be equipped with kilns, presses and spray dryers supplied by Sacmi, Italy’s leading supplier, with handling equipment provided by Tecnoferrari. State-of-the-art inspection, sorting and packing equipment uses Qualitron, Easy Line, and Falcon from System of Italy. System will also supply Rotocolor decoration technology. The delicate press decoration process stage was assigned to LB Officine Meccaniche. Sacmi has already installed the press, ball mills, spray dryer and kilns and other equipment for the ceramic plant.
The massive plant is capital intensive and staffing ratios are low for a facility of this scale, with extensive use of computer systems and process control including the use of laser-guided systems to handle production.
Commenting on the current status of work on the ceramic plant, Mousa says: “With the steel structure erected, work on roof sheeting and wall cladding is 95 per cent. Currently, the fire exit doors are being installed and the finishing touches are being given to the walls of the facility.
“With most of the equipment installed within the ceramics plant, interfacing of the systems and equipment is in progress.The erection of the kiln and dryer chimneys is to be implemented shortly.
“On site, following the completion of the precast boundary walls and with asphalt works and laying of walkways in progress what remains to be completed are the entrance gates and guard rooms. Construction of the power plant (generator room) is complete while the switchgear rooms are being built.”
At the porcelain plant, about 75 per cent of the work on the roof sheeting and wall cladding has been completed and the final paint coats are being applied on the walls. With most of the equipment installed, work is in progress on assembling the spray dryers, he says.
Erection work is under way on an LB-designed technological tower, which weighs about 300 tonnes and stands 28 m high, a distinctive feature of the porcelain plant.
“As far as the electro-mechanical works at the ceramic and the porcelain plants are concerned, all major items like generators, transformers, switchgear have been procured by the contractor and ready for installation and termination. The fire alarm and fire fighting network has been completed, while installation of highbay lighting and plumbing works for toilets are nearing completion. The air compressor has already been procured by the contractor and air network piping works are in progress,” he says.
With a strong team charged with the responsibility of delivering a world-scale project, Future Ceramics is confident that it is well-positioned for success.
“The civil contractor and fabrication contractors are well qualified to execute the job as per standard specification and on time. All contractors working on the project are dedicated and hard working (even working on two shifts sometimes) to hand over the project on time,” Mousa concludes.
With all works drawing to a satisfactory close, Future Ceramics is now aggressively pursuing a marketing strategy that will take its products to the far reaches of the globe.