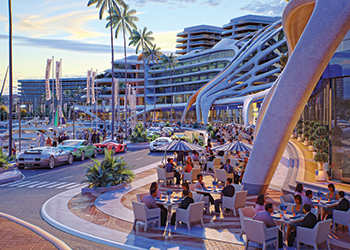

Construction work on the Mondelez Bahrain Biscuit Factory project in Bahrain has reached the halfway mark, with the development targeted for completion in the next three months.
Set to be Mondelez’s largest manufacturing facility in the Middle East, the two-phased project is being built at the Bahrain Industrial Investment Park (BIIP) close to Khalifa Bin Salman Port.
Work on the first phase is being carried out by Mercury Mena, a reputed engineering firm, which has adopted the latest building information modelling (BIM) technology Level Two to implement the project. The company is working in coordination with Tebodin Middle East, the project consultant.
Phase One comprises the main factory in a two-storey building, the main utility and administration buildings, and incoming warehouse, while in the second phase the outgoing warehouse, gate house, ancillary external works and landscaping will be undertaken.
![]() |
The upcoming Mondelez factory. |
Scope of work
Mercury Mena’s scope of work includes construction of the production plant, administration/canteen/utilities (services buildings, gatehouse, fence and gate, internal roads, parking lots and paving, and related external works).
“Once completed, the state-of-the-art facility, which will be spread over 250,000 sq m, will produce 90,000 tonnes of biscuits per year. The first batch of ‘Made in Bahrain’ Oreo cookies, Ritz crackers, belVita, Prince and TUC biscuits as well as Barni cakes is expected to roll off the production line by early 2017,” Ray Howard, project director of Mercury Mena, tells Gulf Construction.
Mercury Mena is responsible for the complete structural works for the project, which comprise the full sub-structure (piles, pile caps and ground beams); superstructure (precast columns, beams and hollow-core roof slabs); all civil works including floor slabs, walls, corrugated cladding sandwich panels, finishes, dock levellers, roads, landscaping and weighbridge.
It will also carry out all the MEP (mechanical, electrical and plumbing) works, which include ammonia chillers and gas boilers for the manufacturing process, HVAC (heating, ventilation and air-conditioning) and fire-fighting systems, and four lifts.
Commenting on the challenges, Howard says: “The construction programme is extremely condensed and the client’s production equipment is being installed concurrently with the construction works, which demands extreme due-diligence and well-planned coordination between all parties.”
To meet the requirements of this world-class industrial facility - a food processing unit with a high production volume - a range of high-specification finishes are being used. Considering the facility will be well-trafficked, for the flooring for instance, the contractor is using power float concrete chemical hardened, floor finish type F4; and heavy-duty resin floor polyurethane, of types F5 and F6 for the factory.
Mercury Mena is involved in the turnkey delivery of highly technical and logistically challenging projects across the region with a client list that includes many Fortune 500 companies.
“The company is a process-driven organisation committed to advanced technology such as BIM. It delivers true value and risk management services through the creation and implementation of procurement strategies tailored to its clients’ requirements,” Howard concludes.